No.3 クレームにどう対処する?
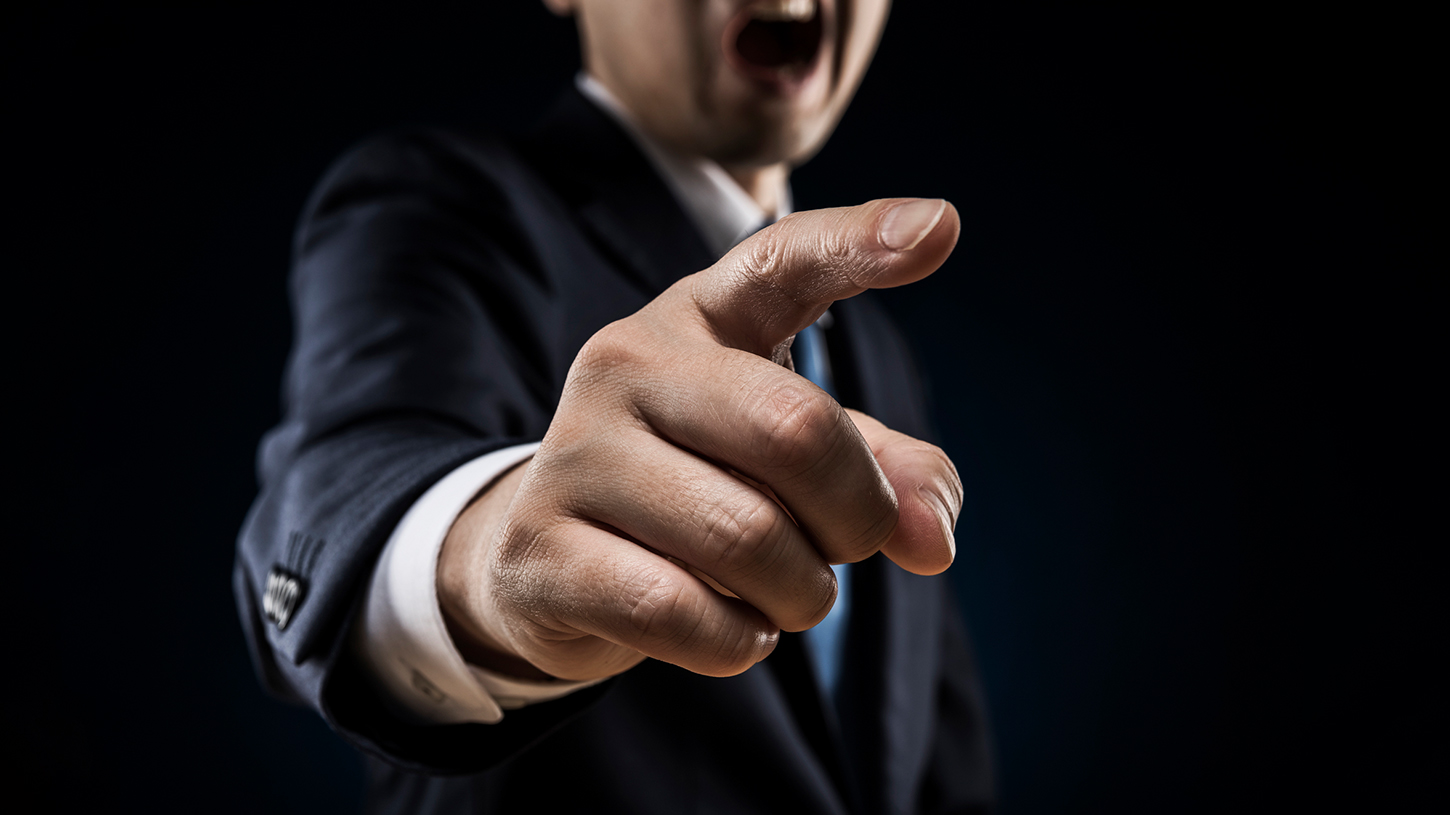
当社は主に水廻り設備のメンテナンスを中心に30年以上に亘って業務を展開してきた。その過程で、いろいろなクレーム案件を多々処理してきた。メンテナンス工事は例えば排水管の詰まりを修理するのも、受水槽の満水警報が発報し、作動不良になったボールタップを交換するのもクレーム処理になる。
当初の会社の業態はこうした案件を処理するメンテナンス工事が主体であったが、実際は客先からの依頼で、メンテナンス工事に絡んだ「クレームを処理する会社」になっていた。初めから、このような業態になることを目指したものではなく、数々のクレーム案件を処理している過程で、依頼されるケースが増えてきた結果、クレーム対応ができる処理会社として、サブコン・ゼネコン各社から認知されてきたものと考える。
なお、配管設備に起因するクレーム調査は、同じ調査でもリニューアル時に実施している「劣化診断調査」とは根本的に異なる。クレーム調査は、その原因も多岐にわたり、しかも、解決には高度な専門性の他、法律的な見識も必要になる。非常に難しい分野である。
また、建設業界(請負業界)特有のパワーバランスが障害になることもある。必ずしも正確な調査結果が業界に生かされるとは限らない。建設業界がなかなか「メーカー」になれきれない理由の一つといえる。
[ クレームの内容 ]
クレームの原因は様々で、大きく分類すると
①設計に起因する事例
②施工ミスによる事例
③メンテナンスミスによる事例
④明らかにメーカーの品質不良による事例
⑤不可抗力による事例
⑥その他
がある。
クレーム案件は時として損害賠償の請求ばかりではなく、信用問題に発展するケースもある。
昨今、PL法や品確法が制定され、コンプライアンスが重視される時代になり、品質管理部門は事業継続の上でも重要な位置を占めるようになってきている。
当社が長年に亘って対処し、処理してきた案件のうち、ここ20年の間で関与したクレームは60件ある。
このうち平成15年から今日までは28件と、増えてきている。
内訳は ①14件(16%)、②16件(19%)、③21件(24%)、④8件(9%)、⑤22件(26%)、⑥5件(6%) となっている <一部重複あり>。
新築時のクレームである①②④の合計は38件で、クレーム調査の半分近くを占めている。
また、⑤の不可抗力の主な原因は微生物障害であり、水配管特有のクレーム案件である。
当社で扱ったクレーム案件で、最も難しい部類に入るのは「メーカーの品質不良~設計ミス」に起因するものである。
メーカーが長い年月をかけて研究・開発し、自信を持って販売した新製品でも100%満足できるものとは限らない。
取り扱い説明書(マニュアル)を製品に添付しても、十分その製品を理解しないまま使用されたり、勝手に理解したと思い込んで使用されることもある。また製品が設計ミスのまま販売され、消費者からメーカーにクレームがあり、初めてその欠陥に気付くこともある。メーカーはあらゆる事項を想定した製品作りを行っているが、万一クレームがあった場合、そのクレームをを「ノウハウ」として製品の改良に生かし、更に『完成度』の高い製品にしようと努力する。こうしたノウハウを蓄積した製品は市場を独占することができる。
[クレーム案件の処理例]
竣工2年目にテナント工事で増設したSP管(白管)が供用12年目に腐食によりネジ部から漏水し、漏水場所がコンピュータのサーバールームであったため、大きな問題となった。
増設に際し、主管から分岐管の取り出しには、「不断水工法」で施工しなければならなかった。
当初、液体窒素による「凍結工法」での施工を想定したが、現場内での火気使用ができず、K社の不断水工法用の「特殊継手」を使用することとなった。この特殊継手の直近の増設部から水漏れが発生した。
同じような特殊継手は他に何箇所か採用していたので、オーナー側は非常な不安を抱えたため、施工したサブコンに原因を究明するよう指示があった。
サブコン担当者は以前から「当社は工事だけでなく、調査も出来る会社である」と認識していたため、調査依頼の話が来た。
当社では今回の漏水事故に対し、ことの重要性にかんがみ、下記のような手法で調査に着手した。
(1)溶存酸素測定及び計量分析(水質分析・堆積物分析)
(2)X線回折分析(堆積物物分析)
(3)撤去したSP管の内視鏡調査
(4)同上サンプリング調査
(5)X線撮影(主に配管ネジ部)
出揃ったデータを解析した結果、「局所濃淡電池形成に伴う、電位差腐食」であることが判明した。
切削クズ、錆、堆積物、付着物やスケールなどの析出物により、配管表面に金属イオン濃度の濃淡による局所電池が形成される。その影響により、付着物を中心として局所的な腐食と、その周辺に二次的な腐食を引き起こす。この場合には、わずかな鉄片が亜鉛メッキ層に穴を開けることが可能なため、本案件の原因である可能性が最も高い。
その根拠として、
①サンプリング管の半割した一方を酸洗いしたら、管内面に孔食が点在している。
②腐食は管底に極端に集中している。
③腐食の真上にはスケールが堆積している。
の3点が挙げられるからである。
鉄片・鉄クズの発生源については不明であり、主管施工時の残渣物が滞留した可能性もある。
しかしながら、何箇所もある増設部のうちで、腐食が生じた系統と、問題ない系統との違いはこの「特殊継手」を使用しているか、否かだけである。
メーカーは否定しているが、火薬の力で瞬間的に配管部を切断するという特性上、切削クズや鉄クズが全く発生していないとは断言できない。実際、この製品のカタログでは瞬間的に「異常圧」が掛かるので、分岐直後の配管には「ボールバルブ」を取り付け、必ず「閉」の状態で開通させることを強く推奨している。
なお、余談になるがメーカーへの問い合わせの際、「ハンマーで叩くとき、体勢が悪かったり、躊躇したりすると、爆発力が弱まり、半開きのままの状態で刃がとまってしまうことが少なからずある」との説明があった。
この場合、切削片が増設した系内に進入する可能性がある。カタログには必ず「ボールバルブ」を取り付けるよう明記されているのはこのためと思われる。
「局所濃淡電池形成に伴う電位差腐食」がこの現場の原因である場合、腐食の発生源になった鉄片はどこから来たのか不明である。
さて皆さん。原因がこの「特殊継手」であった場合、この継手を製造・販売しているメーカー側に非があるのか、それとも実際この継手を使用した工事業者に責任があるのか、判断できますか?
これはほんの一例であるが、これまで調査した案件の中には非常にドラマチックな展開になった例もある。
タイトルが「社長の現場レポート」なのだから、現場でのクレーム案件の事例をいろいろご紹介したいところであるが、web 上で公開するには不向きな事柄であるので控えたいと思う。
また、クレーム対応の調査を行う場合、依頼された案件が依頼者側の瑕疵によることもあり、当社としても難しい対応に迫られる場合もある。調査報告書を提出する際は、依頼者に配慮しつつも、当社の信用を汚すことがないように心がけている。
当社のキャッチフレーズは Reserch ・ Engineering ・ Maintenance であり、調査から原因を突き止め、その解決法を提示し、施工・管理までトータルに行える日本で唯一の会社を目指しております。
調査(分析・配管の劣化診断等)では優れた会社が数多くありますが、解決方法を提示できる会社はありません。残念ながら、建築業界では調査会社と工事会社とは別のものであるという固定観念があります。
クレーム案件は「正確な調査」が行われて初めて「確実な施工」ができるものです。分析会社はデータを作成することが主な業務で、そのデータを読み取る力は多くの現場経験を必要とします。残念ながら分析会社に分析以上のものを要求しても、彼らも困りますし、問題は解決しません。
「調査ができる会社」と「分析業者」とは必ずしも同一ではないということを再認識する必要があります。
当社は「調査会社」としての顔もあれば、「工事会社」としての顔もあります。依頼があれば設計段階でメンテナンスについてのご提案もさせていただきます。30数年直接現場に携わってきた会社として、少しでも業界の役に立つ業務を提供していきたいと考えております。
何なりとご相談下さい。